Lost wax casting, an ancient yet profoundly modern technique, is at the heart of Taiyuan Simis Investment Casting Co., Ltd.'s manufacturing services. As a leading lost wax casting foundry, we have refined this intricate process to deliver precision and excellence across diverse industries. Our lost wax casting service offers unparalleled accuracy and the ability to create complex, detailed parts that few other methods can achieve. This capability stems not only from our deep-rooted expertise but also from our commitment to embracing cutting-edge technologies and maintaining high-quality standards.
At Taiyuan Simis, we understand the critical role that high-quality casting plays in the success of our clients' projects. Whether it's creating intricate jewelry, precise aerospace components, consumer electronic components, auto parts, railway components, artworks, or durable medical devices, our process is designed to meet the unique needs of each application. By providing a comprehensive lost wax casting service, we enable innovators and manufacturers to transform their visions into tangible products. In this article, we will explore what you should expect when partnering with a top-tier lost wax casting foundry like Taiyuan Simis, from the choice of materials to the breadth of applications and the detailed steps that ensure every cast meets our exacting standards.
Overview of the Lost Wax Casting Process
The lost wax casting process, also known as investment casting, is a precision manufacturing technique that has been employed for thousands of years and continues to be essential in producing detailed, high-definition geometries in modern industry. At Taiyuan Simis Investment Casting Co., Ltd., our lost wax casting service meticulously follows a sophisticated process to ensure exceptional outcomes:
Wax Model Creation: Our lost wax casting service starts by creating an exact wax replica of the desired final product. This wax model, formed either by injecting molten wax into a metal die or hand-sculpting, is crucial as it needs to precisely replicate every detail and dimension of the intended part, including internal features.
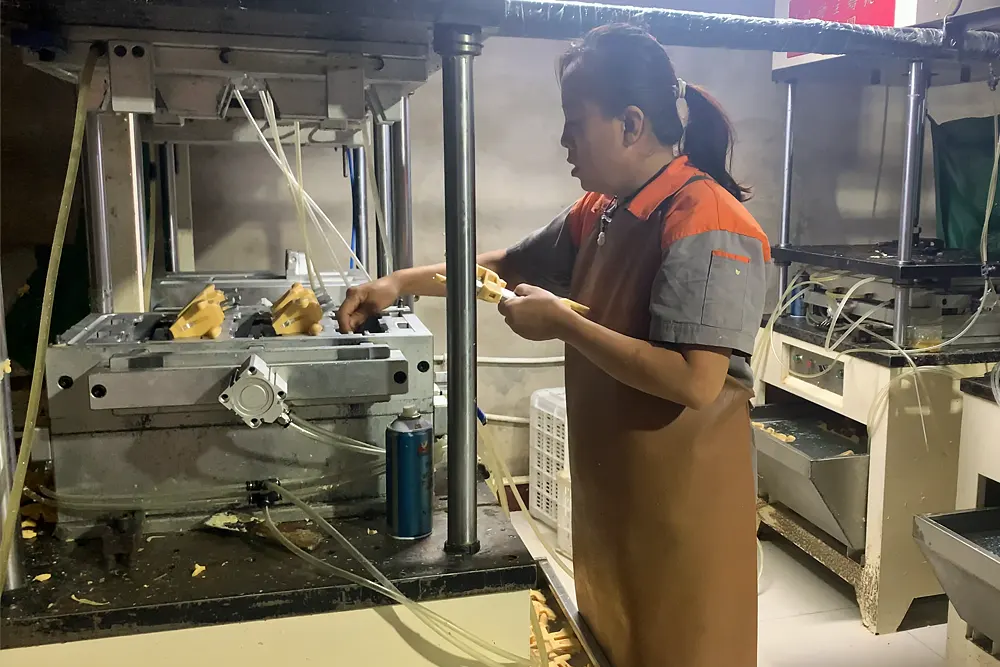
Tree Assembly: The wax models are then attached to a central wax sprue, forming a "tree." This assembly is essential, as it defines the pathways for the molten metal to flow and fill the cavities left by the wax models during casting.

Shell Building: The wax tree is dipped multiple times into a ceramic slurry, then sprinkled with fine sand. Each layer is allowed to harden and dry before the next is applied, gradually forming a robust ceramic shell capable of withstanding the molten metal during the casting phase.
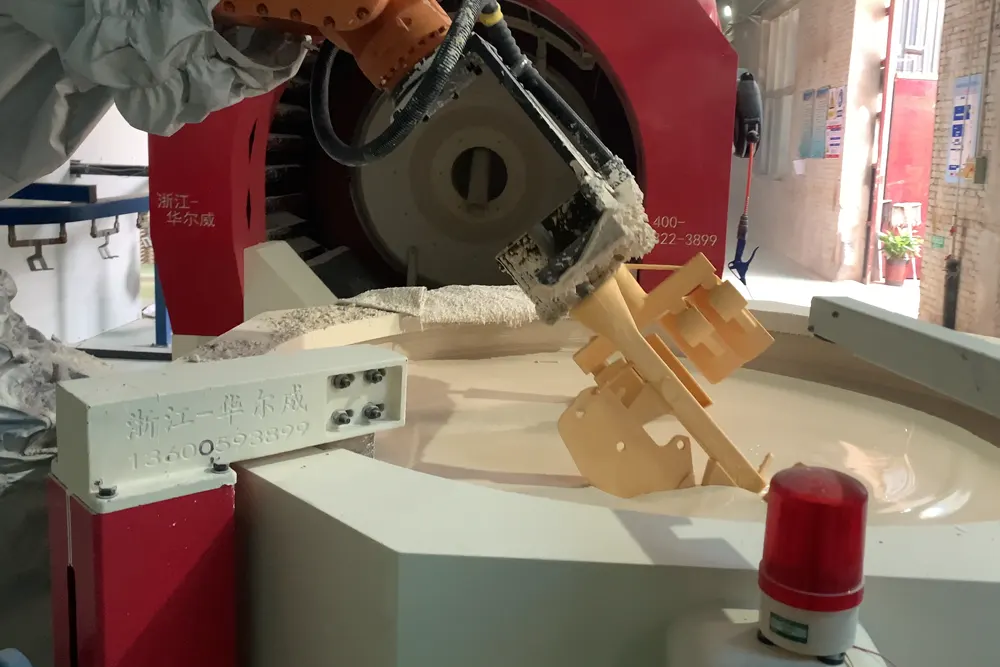
Wax Removal: Once the ceramic shell has fully hardened, the wax is melted out, typically in an autoclave, leaving a hollow ceramic mold. This critical step in our lost wax casting service is where the technique gets its name and is key to achieving the precise details in the final casting.

Metal Pouring: The empty ceramic mold is preheated to eliminate any residual wax traces and to strengthen the mold before pouring in the molten metal. At Taiyuan Simis, the temperature and composition of the metal are meticulously controlled to ensure optimal flow and solidification properties.

Cooling and Shell Removal: After the metal has cooled and solidified, the ceramic shell is carefully broken away to reveal the cast metal parts, still attached to the central sprue. This stage marks the culmination of the lost wax casting process.

Cutting and Finishing: Finally, the individual parts are separated from the sprue and undergo additional finishing processes such as heat treatment, machining, sanding, and polishing, tailored to meet the specific requirements of each part and its application.

Throughout each step of our lost wax casting service, Taiyuan Simis maintains the highest standards of precision and quality control, leveraging our extensive experience as a leading lost wax casting manufacturer. This rigorous attention to detail enables us to deliver superior-quality parts that consistently meet the stringent specifications of our diverse client base across various industries.

Material Grades for Lost Wax Casting
In our lost wax casting service at Taiyuan Simis Investment Casting Co., Ltd., we utilize a variety of material grades to cater to the specific needs of our diverse clientele. Each material is selected for its unique properties and suitability for different applications, ensuring that every product delivered meets the highest standards. Here, we'll delve into the specific material grades commonly used in our lost wax casting service and discuss their applications and benefits.
Stainless Steel: For our lost wax casting service, stainless steel is a popular choice due to its corrosion resistance and strength. Grades like 304 and 316 are frequently used; 304 is known for its versatility, while 316 offers higher corrosion resistance and is preferable in marine and acidic environments. For more demanding applications, we use 17-4 PH stainless steel, which provides an excellent balance of strength and corrosion resistance after heat treatment.

Aluminum Alloys: Aluminum alloys are favored in our lost wax casting service for their lightweight and superior machinability. A356 is a common choice for its good casting and welding properties, making it ideal for automotive and aerospace parts. Another frequently used alloy is AlSi10Mg, which offers a good strength-to-weight ratio and excellent corrosion resistance, suitable for complex thin-walled castings in aerospace and automotive industries.

Carbon Steel: Various grades of carbon steel are used in our lost wax casting service depending on the strength and hardness requirements. Low carbon steels such as 1020 are used for parts requiring good ductility and weldability. For higher strength and wear resistance, medium carbon steels like 1045 are employed, especially in the manufacturing of industrial machinery and automotive components.

Tool Steels: In our lost wax casting service, tool steels such as D2 or A2 are chosen for their high hardness and ability to retain a cutting edge at elevated temperatures. These steels are ideal for producing cutting tools, dies, and molds that require high wear resistance and toughness.
Titanium and Nickel-based Alloys: For applications demanding high strength, lightweight, and exceptional corrosion resistance, our lost wax casting service often turns to titanium alloys like Ti 6Al-4V. This grade combines durability, heat resistance, and biocompatibility, making it perfect for aerospace, medical, and automotive applications. Nickel-based alloys, such as Inconel 718, are used for their ability to withstand extreme environments, making them ideal for aerospace and power generation components.

Our lost wax casting service is equipped to handle these diverse materials, enabling us to produce parts that meet specific performance criteria across a range of industries. At Taiyuan Simis, we understand that the material grade is critical to the success of the finished product, and our expertise in selecting the right material ensures that each casting achieves the desired properties and performance. Through rigorous quality control and advanced manufacturing techniques, our lost wax casting service provides reliable, high-quality castings that consistently meet the demanding standards of our clients.
Applications Covered By Our Lost Wax Casting Service
Our lost wax casting service at Taiyuan Simis Investment Casting Co., Ltd. is crucial for producing critical components across a spectrum of heavy industries, where precision and durability are paramount. Each sector benefits from the specific applications of lost wax casting, leveraging the versatility and precision this method offers.
Heavy Machinery Components: In the realm of heavy machinery, our lost wax casting service is used to manufacture parts like gears, bearings, and housings. These components must endure intense operational stress and wear, making the precision and material integrity provided by lost wax casting essential for long-term durability and reliability.

Train and Railway Components: The railway industry relies on our lost wax casting service for the production of complex parts such as brake assemblies, coupling mechanisms, and door components. These parts are critical for the safety and efficient operation of rail systems, requiring high precision to ensure proper fit and function under the stresses of constant use.

Oil Pipeline Components: For the oil and gas industry, our lost wax casting service produces components like valve bodies, pump impellers, and connectors that are crucial for managing the flow and pressure within pipelines. These parts are made from corrosion-resistant materials to withstand harsh chemicals and environments, ensuring long-lasting performance and safety.

Mining Components: The mining sector demands rugged and robust components capable of withstanding abrasive environments. Our lost wax casting service delivers large carbon steel castings for applications such as drill heads, excavator teeth, and wear plates. These parts are specifically designed to resist wear and impact, prolonging the equipment's life and reducing downtime.
Construction Machinery Parts: In construction, large carbon steel castings produced by our lost wax casting service include structural components, engine parts, and hydraulic system components. These parts must not only support the heavy loads but also resist the environmental elements they are exposed to daily. The accuracy and strength of the castings ensure that the machinery operates reliably and efficiently, crucial in a sector where equipment failure can result in significant project delays and increased costs.

By focusing on these industrial applications, our lost wax casting service provides tailored solutions that meet the stringent requirements of each sector. At Taiyuan Simis, we understand the critical nature of these components and the role they play in the overall safety and functionality of heavy-duty machinery and infrastructure. Our commitment to precision in casting translates into enhanced performance and dependability of the components we produce, reinforcing the trust our clients place in our capabilities.
Major Advantages of Lost Wax Casting
Lost wax casting, offered by Taiyuan Simis Investment Casting Co., Ltd., is a highly regarded process known for its versatility and precision, making it indispensable across various industries. This technique provides several key advantages that distinguish it from other metal forming processes:
High Precision and Detail: Lost wax casting is renowned for its ability to produce components with intricate details and complex geometries that other casting methods cannot match. This precision is crucial for applications requiring exact specifications and fine features, such as in medical implants or aerospace components. Taiyuan Simis utilizes advanced wax modeling and mold-making techniques to ensure that every nuance of the original design is captured accurately.
Excellent Surface Finish: The smooth surface finish achievable with lost wax casting reduces the need for additional machining and finishing processes, which can significantly lower production costs and time. The quality of surface finish provided by Taiyuan Simis ensures that components meet aesthetic as well as functional standards right out of the mold.

Versatility in Material Selection: Lost wax casting service at Taiyuan Simis supports a wide range of materials, including various grades of steel, aluminum, titanium, and precious metals. This versatility allows for the production of parts tailored to specific properties such as strength, ductility, corrosion resistance, and weight, enhancing the final product's performance and durability.
Ability to Produce Complex Parts: The lost wax process excels in manufacturing parts with undercuts, hollow sections, and complex internal structures without compromising structural integrity. This capability is beneficial for producing parts like turbine blades, gear housings, and engine components for the automotive and aerospace industries.
Consistency and Reproducibility: Taiyuan Simis ensures high repeatability with minimal variability between parts, which is essential for large productions where consistency is critical. Our rigorous quality control processes and meticulous attention to detail in every step of the casting ensure that each batch maintains uniform quality and specifications.

Minimized Material Waste: The precision of the lost wax casting process results in minimal waste, as materials are only used where needed. This efficiency not only reduces material costs but also aligns with sustainable manufacturing practices by minimizing environmental impact.
These advantages underscore why Taiyuan Simis Investment Casting Co., Ltd. is a leader in the lost wax casting industry. Our commitment to leveraging this sophisticated casting technique ensures that we deliver superior quality products that fully meet our clients' specifications and exceed their expectations in performance and reliability.
Technical Challenges and Solutions
The lost wax casting process, while highly effective for producing complex and precise components, presents several technical challenges. At Taiyuan Simis Investment Casting Co., Ltd., we have developed targeted solutions to overcome these challenges, ensuring our lost wax casting service maintains the highest standards of quality and reliability.

Wax Pattern Integrity: One of the primary challenges in lost wax casting is maintaining the integrity of the wax pattern throughout the mold-making process. Distortions or imperfections in the wax model can lead to defects in the final cast. To mitigate this, Taiyuan Simis employs advanced wax injection equipment and high-quality waxes that maintain stability under varying conditions, ensuring that the wax patterns accurately replicate the desired geometries.
Ceramic Shell Cracking: The ceramic shell must withstand high temperatures and the stress of molten metal without cracking. Our solution involves optimizing the ceramic slurry formulation and employing controlled drying and curing techniques that enhance the shell’s strength and thermal shock resistance. This meticulous approach minimizes shell failures and ensures the integrity of the final casting.
Metal Flow and Solidification: Achieving optimal metal flow and solidification is crucial for ensuring the mechanical properties and surface finish of the casting. Taiyuan Simis utilizes simulation software to predict and optimize metal flow, gating, and risering systems. This preemptive analysis helps in identifying potential cold shuts and misruns, allowing for adjustments before actual casting, thus reducing waste and improving yield.
Porosity and Inclusions: Porosity and inclusions within the cast parts can compromise their structural integrity and aesthetic quality. To combat this, our lost wax casting service incorporates refined melting and pouring practices, including the use of high-purity metals and advanced degassing techniques. Additionally, we implement rigorous process controls during the slurry making and dipping stages to prevent contamination and ensure a clean, inclusion-free ceramic shell.
Post-Casting Finishing: Achieving the desired finish on complex shapes can be challenging due to the intricacies of the parts. Taiyuan Simis has invested in state-of-the-art finishing technologies, including CNC machining, and automated polishing systems. This not only improves the precision of the final dimensions but also enhances the surface quality of the cast parts.
Quality Control: Ensuring consistent quality across batches in lost wax casting is paramount. At Taiyuan Simis, our quality control process is comprehensive, involving dimensional inspection, non-destructive testing, and mechanical property testing. Our ISO-certified procedures ensure that every casting delivered meets our high standards and the specific requirements of our clients.

By addressing these challenges head-on, Taiyuan Simis ensures that our lost wax casting service delivers superior results, even in the most demanding applications. Our commitment to continuous improvement and innovation in solving casting challenges sets us apart as a leader in the foundry industry.
Selecting a Lost Wax Casting Provider
Choosing the right provider for lost wax casting services is crucial for the success of your manufacturing projects. The quality of the cast components can significantly impact the overall performance and reliability of the final product. Here are key factors to consider when selecting a lost wax casting provider, emphasizing the capabilities of Taiyuan Simis Investment Casting Co., Ltd.

Experience and Expertise: The provider's experience in the industry is a fundamental criterion. Look for a foundry like Taiyuan Simis, which has a long-standing history and proven track record in lost wax casting. Our expertise ensures that we understand the nuances of the process and can handle complex projects across various industries effectively.
Material Knowledge: An adept lost wax casting service provider must have extensive knowledge of different material grades used in the process. Taiyuan Simis offers a wide range of materials, including stainless steel, aluminum alloys, and specialty metals, catering to specific application needs and ensuring optimal performance of the cast parts.
Advanced Technological Capabilities: The technological infrastructure of the foundry is critical. Taiyuan Simis is equipped with state-of-the-art equipment and technology for both creating precise wax models and performing advanced metal casting. This capability allows for high accuracy, superior surface finishes, and consistency in production.
Quality Assurance: Verify that the lost wax casting manufacturer implements stringent quality control measures. Taiyuan Simis adheres to ISO 9001 quality standards, ensuring each part undergoes rigorous testing and inspection processes. This commitment to quality helps in minimizing defects and ensuring that parts meet or exceed customer expectations.
Customization and Flexibility: The ability to adapt to client-specific requirements is essential. Taiyuan Simis excels in providing customized casting solutions, demonstrating flexibility in handling various sizes, complexities, and production volumes. Whether you need a few specialized parts or large-scale production runs, the provider should be able to accommodate your needs.
Turnaround Time and Pricing: Efficient production times and competitive pricing are also important considerations. Taiyuan Simis offers cost-effective solutions without compromising on quality or deadlines, ensuring that your projects are completed on time and within budget.
Customer Service and Technical Support: Lastly, responsive customer service and robust technical support are indicative of a reliable provider. Taiyuan Simis prides itself on offering comprehensive support throughout the casting process, from initial consultation to post-production services, ensuring a smooth and satisfactory experience for clients.
By considering these factors, you can make an informed decision when selecting a lost wax casting service provider. Taiyuan Simis Investment Casting Co., Ltd. stands out as a premier choice, dedicated to delivering exceptional quality and service in every project.
Conclusion
The lost wax casting service provided by Taiyuan Simis Investment Casting Co., Ltd. exemplifies our commitment to excellence and innovation in the casting industry. Our mastery of this ancient yet advanced technique allows us to offer unmatched precision, versatility, and quality, making us a preferred partner for industries requiring highly detailed and complex components. The major advantages of lost wax casting, such as high precision, excellent surface finish, and the ability to handle diverse materials and complex geometries, position this method as an indispensable solution for manufacturing challenges across sectors like aerospace, medical, automotive, and beyond.
At Taiyuan Simis, we pride ourselves on not just meeting but exceeding customer expectations through our rigorous quality control, advanced technologies, and a deep understanding of the lost wax casting process. Our ability to deliver cost-effective, high-quality, and custom solutions ensures that our clients receive the best possible outcomes for their projects. As we continue to innovate and refine our capabilities, Taiyuan Simis remains dedicated to advancing the potential of lost wax casting to meet the evolving needs of modern manufacturing.
Whether you are looking to develop intricate components for critical applications or seeking a reliable production method for high-performance parts, Taiyuan Simis is equipped to guide you through every step of the process. We invite you to experience the benefits of partnering with a leader in lost wax casting services, where your ma